A big wooden work on commission
A wooden bridge commissioned by a private Azerbaijani that saw its completion after being designed about a decade ago by Israeli architects, thanks to the entrepreneurship of Francesco Carullo. The latter assembled a team that with a year of work, realized this important work in the Baroque style.
It is a crosswalk bridge placed in a private villa in Baku, the capital of Azerbaijan, on a cliff of the Caspian Sea. The bridge has a steel structure supplied directly by the client on which wooden parts were designed for decking and decoration.
PROJECT DETAILS
Client: Private
Design: Aviva Benari, Oden Halaf
Materials: Steel (supporting structure), Okumè marine plywood (boarding) and Burma Teak wood (decors)
Execution:CAD design, product development, CAM programming, cnc machining, finishing, assembly
Dimensions: 14 x 3 x 3 m(l x w x h)
Year: 2020
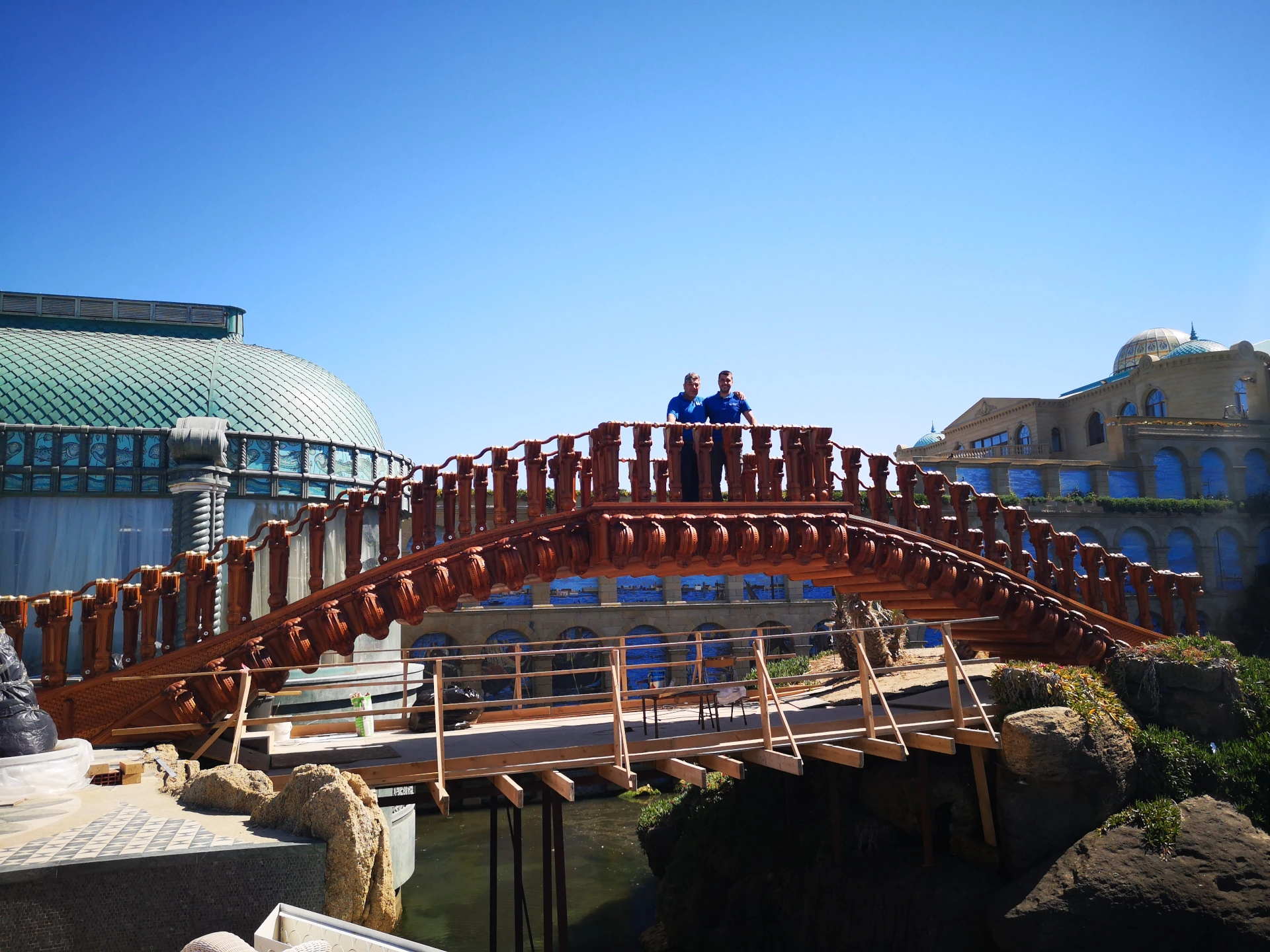
The stylistic study and concretization of the work
Through the study of Professor Angelo Catano, art historian, the concretization of the work in the Baroque style in its best sense was achieved. The definition and continuum of the decorative apparatus, the solution of details not contemplated in the project, the study and implementation of a digital program generated through CAM software capable of guiding the numerical control in the machines in the company were priorities in the chapter preparatory to the demanding phase of the implementation of the site for carpentry and cabinetry. After reviewing with the designers the design part and that on the possible problems of the process of making and adapting the forms, the stylistic and historical research on volumes and sculptural lines was carried out. The parts were drawn in a real digital sculptural process with organic modeling software by Simone Rasetti, a digital sculptor. Technical/artistic verifications of the created decorative parts are essential for structural feasibility, allowing the created 3D model to be prototyped without errors. At the end of the creative part, the digital sculptor has complex Mesh on his software, these make the three-dimensional management of the files difficult on the production stage of prototyping.
The choice of materials and the engineering of the work
To create the support structure, we chose to use phenolic okumè plywood, widely used in the nautical sector, which combines excellent performance in terms of mechanical resistance and stability over time with high resistance to degradation. Embracing means a load-bearing substructure, which has a triple function: to improve the tolerance level of the structure, to constitute a mask with univocal references and to act as an anchoring structure for the teak components. The decorative parts were made of Burma Teak wood, a material that tolerates very well temperature excursions, humidity, saltiness and atmospheric agents. The decorative elements cover the entire load-bearing structure and are fixed to the bridge using the face of the component that remains hidden; consequently, all the fixings are not visible. The components decorated with the fish scale and bubble textures were made with okumè plywood panels.
The entire work was designed, with the help of CAD software, by CAD designer Simone Carullo in order to optimize it as best as possible. The bridge consists of 1143 components.
From drawing to numerical control
3D digital models of the project, in solid model formats, Nurbs surfaces and mesh, were imported into Alphacam CAD-CAM software. The purpose of this software is to generate the tool paths by taking advantage of the strategies made available for programming. More than 850 hours of machining time were required for the fabrication of all components on the machine.
Given the large number of components, systems for clamping the parts onto the machine table were designed that would reduce machine downtime to a minimum but, at the same time, ensure decimal accuracy of the components. This machining phase was carried out by Francesco Carullo, master craftsman and business owner, who, thanks to his skills and 30 years of experience in the CNC machine sector, was able to create machining strategies congruent with the all new requirements of a job that no one else in 10 years had been able to accomplish.
The finish
At the end of sanding, a finishing coat was applied by brush, using specific oil for teak. The oiling operation should be carried out about every 6 months, so as to preserve the preservation and natural design wood effecto.
Laying
Upon completion of the machining and test assembly at the company premises, all components were carefully packed and stored inside fourteen wooden crates prepared for road transport. Francesco and Simone Carullo traveled to Baku and assembled the work on site. Within fifteen days, the entire bridge was reassembled at its final destination, also completing the final touches related to painting and caulking the joints. The work is placed in an elevated artistic context, surrounded by mosaics and marble workings; it also fits into an equally interesting naturalistic setting: in fact, the bridge serves as a link between the green spaces of the villa and the outbuilding located on the cliff, overlooking an inlet of the Caspian Sea.
This is custom heading element
The volume, published by D’Abruzzo Edizioni Menabò, contains the story of two years of work told through the texts of the designers and an extensive photo gallery. In charge of the book’s editorial and stylistic design was graphic designer Francesca Carullo, who personally oversaw every stage of the project. Her work highlighted every aspect of the work paying homage to a work that is an expression of artistic craftsmanship and Made in Italy. All the steps, from design to installation, are defined in detail in the text. The photos shown help to understand the majesty of the work created, but also to appreciate the operational difficulties, the expertise, the skill, and the mastery of the workers. The book is aimed at professionals in architecture, engineering and art history , but also at enthusiasts interested in learning what lies behind such an important work. The book can be purchased at dabruzzo.it and at the Mondadori Point bookstore in Orsogna (CH), Piazza Mazzini n.35.